Thermoformed Vs. Extruded Tube Settlers
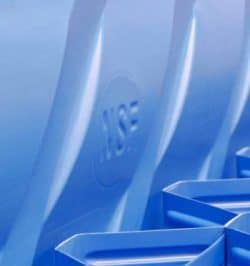
Tube settlers use multiple tubular channels, which are adjacent to each other and sloped at nominal 60˚ angles, to form an increased effective settling area. This configuration allows for a shorter particle setting depth, and as the tube settler channels collect solids, they form a compact mass that promotes the solids to slide down the channel. Tube settlers are an inexpensive method of upgrading existing clarifiers and sedimentation basins by allowing increased flow rate and/or improved performance. They can also reduce the footprint of new clarifier construction.
Thermoformed Tube Settlers
There are many different types of tube settlers on the market, with variations in channel shape, material of construction, and manufacturing method. Brentwood produces tube settlers using the thermoforming process, which differs from the extrusion process. Thermoforming utilizes a flat sheet of plastic that gets heated up inside of a mold to be formed into a specific shape. The formed shape differs slightly between manufacturers, but in general, the flat sheet of plastic is molded into a series of corrugations. These corrugations result in the tube channels once the individual sheets are bonded together. Many manufacturers assemble the corrugated sheets directly together, and others will insert a flat sheet of plastic in between the corrugated sheets for added rigidity and strength. Brentwood takes this a step further by thermoforming structure into the flat sheet to create a “wave sheet”, providing increased rigidity over the simple flat sheet.
Extruded Tube Settlers
The extrusion process takes a raw material (PVC, Polypropylene, etc.), heats it up to its melting point, and pushes it through a die to create a specific shape. The shape for most extruded profiles is generally a “V” or “U” with a tongue and groove on either side. After the shapes are extruded, they are assembled side by side and front to back, using the tongue and groove to connect them together, resulting in a chevron pattern. This type of design ends up providing tubular channels much the same as the thermoformed tube settler.
While performance of each type of tube settler is similar, there are other considerations that differentiate the two types. Since the assembled tube settler product is low weight but high volume, shipping can be very expensive. For this reason, the product is often shipped as individual thermoformed sheets or extruded profiles nested together so the shipping volume is significantly reduced. The product is then field assembled prior to installation.
Assembly Process
The assembly method is a big differentiator between thermoformed and extruded tube settlers. Brentwood tube settlers are assembled using 5 corrugated sheets and 5 wave sheets to make a 1-foot-wide (305 mm) module. The length of the sheets determines the length of the assembled product, which Brentwood offers in 6-foot (1,829 mm), 8-foot (2,438 mm), 10-foot (3,048 mm), and 12- foot (3,658 mm) increments.
Extruded tube settler assembly requires sliding individual profiles together using a tongue-and-groove connection. Typically these tube settlers are assembled into 3’-3” wide x 3’-3” long (1 m x 1 m) modules. The shape and size of the profile will determine the number of profiles required to make an extruded tube settler module. In general, one module of this size will require approximately 100 individual profiles. Based on the number of profiles (approx. 100) needed for one extruded tube settler module of 1 m2, compared to the number of sheets (10) required for one Brentwood thermoformed module of similar size, it can be reasonably estimated that the assembly rate and cost of labor to assemble an extruded tube settler is up to 10x that of a thermoformed tube settler.
Wave Sheets
In addition to the assembly rate, another significant difference with extruded tube settlers is the lack of a wave (or flat) sheet. The wave sheets within a thermoformed tube settler module provide beam strength that is not present in the extruded tube settlers. The benefit of this increased beam strength is that a Brentwood tube settler can span up to 8 feet (2,438 mm) unsupported and still maintain its structural integrity, resulting in minimal supports required for the overall installation. Because of the weakness in the extruded tube settler design they will require a more robust and complex support system, which carries higher material and installation costs.