Non-Metallic Scraper System Revives Aging Water Authority Sedimentation Tank
Addressing structural concerns with a corrosion-resistant, low-maintenance solution tailored for wastewater applications.
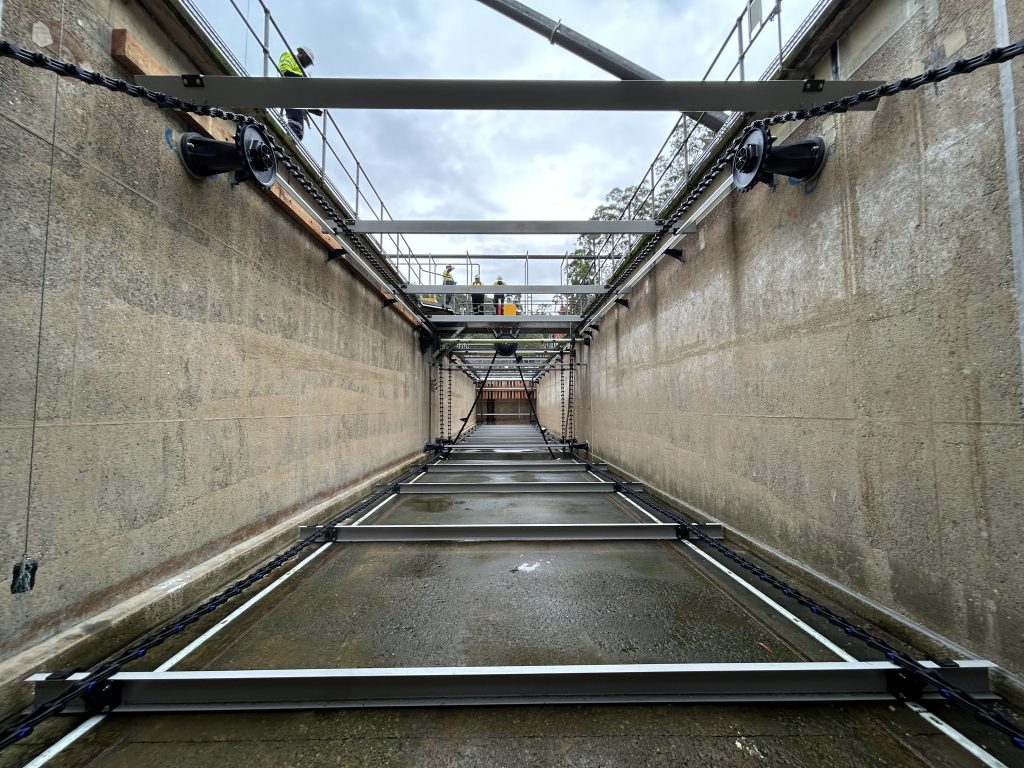
Tank Enviro was awarded the contract to design and supply a non-metallic scraper system, utilising the Polychem system from Brentwood Industries (USA). To support the design process, TES conducted a 3D scan of the existing civil structure, enabling our engineering team to develop accurate as-built models. These models were then used by Polychem’s engineering team in the USA to finalise the system design.
Project Requirements
Following a comprehensive condition assessment, the existing scraper system was found to be at the end of its service life. The original installation featured outdated steel shafting and rails, both heavily corroded, leading to ongoing maintenance issues.
The plant operations team had reported intermittent breakdowns caused by material degradation and equipment misalignment, prompting the need for a complete system replacement with a more durable and low-maintenance solution.
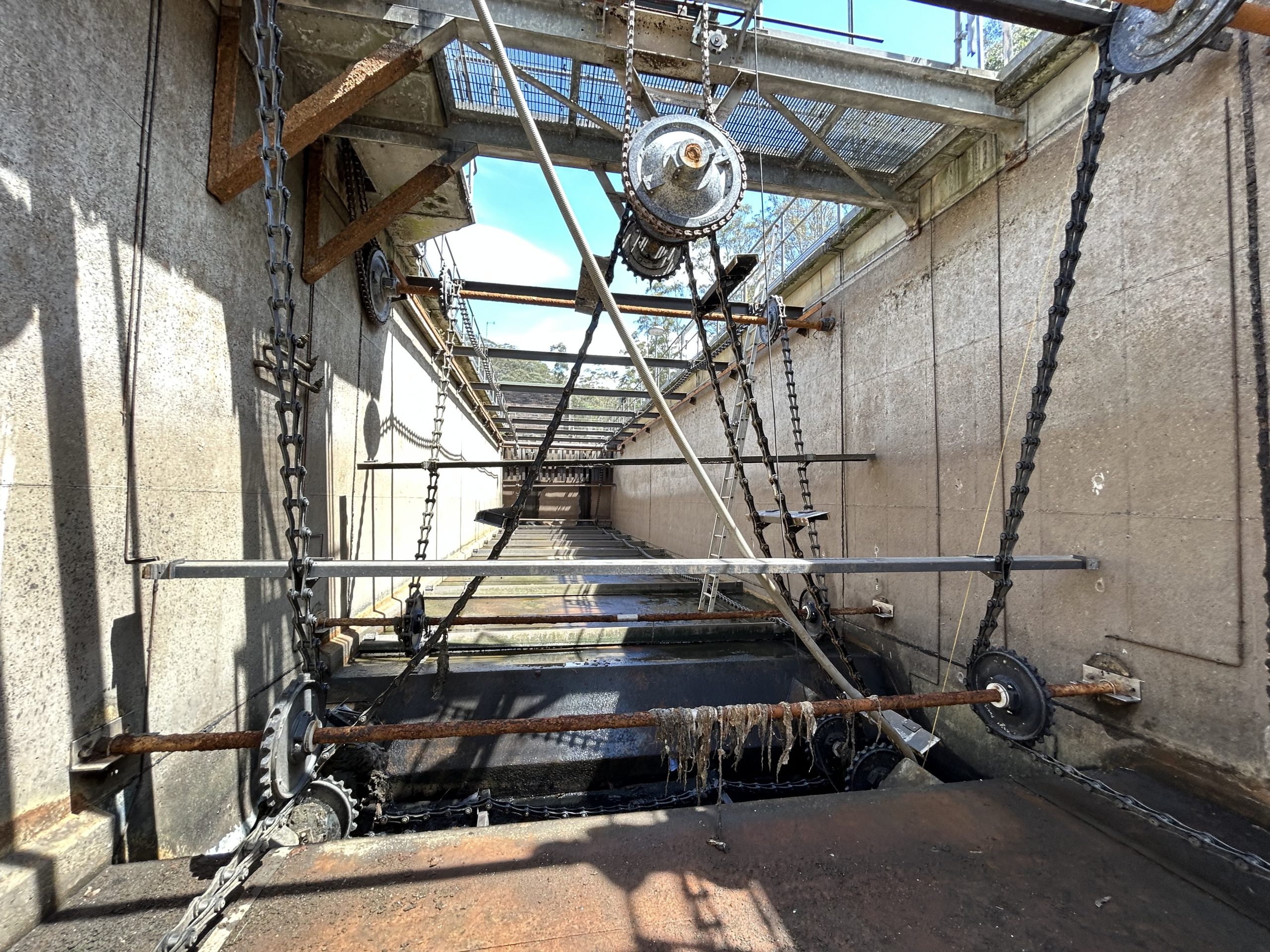
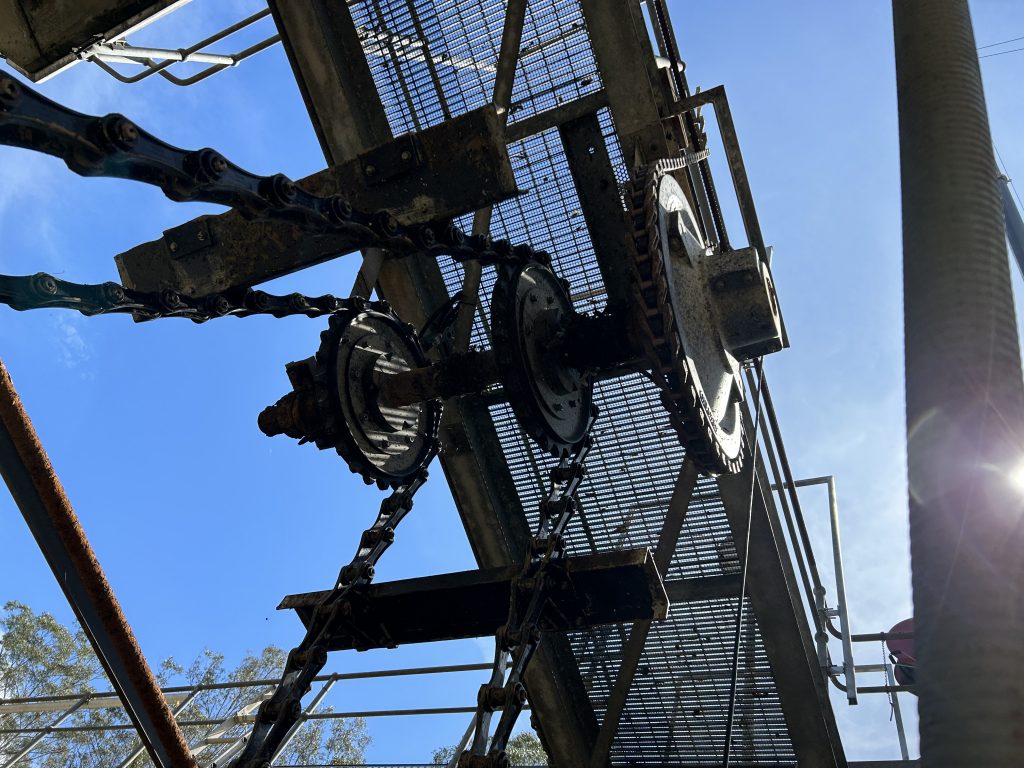
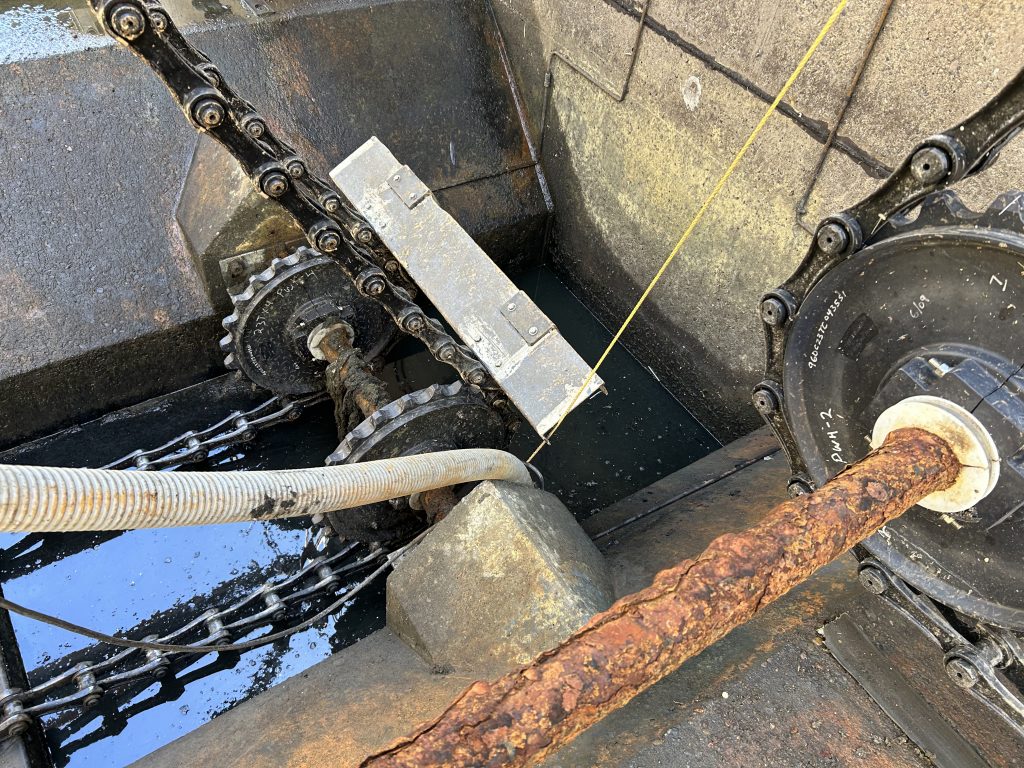
Equipment
- Polychem non-metallic flight and scraper system components (Brentwood Industries, USA)
- Non-metallic chain and wear components
- Sprockets, shafts, and support hardware
- Polychem guide rails and tracking system
- Fasteners, fittings, and installation accessories
Labour and Services
- 3D scanning of the existing secondary sedimentation tank
- Development of accurate as-built drawings for design integration
- Engineering review and coordination with Brentwood Industries
- System layout and design validation for retrofitting into existing tank
- Project management and procurement of all system components
Solution
With limited existing documentation of the secondary sedimentation tank, one of the key challenges was the lack of reliable drawings for design purposes. TES resolved this by performing a high-precision 3D scan of the structure, enabling accurate modelling and seamless integration of the new Polychem system. Collaboration with the plant team was also essential in establishing critical operating parameters, such as minimum and maximum water levels—vital for ensuring the return flights function correctly in directing scum to the collection canoes at the end of each bay.
In addition, the plant lacked condition monitoring for the scraper system. TES addressed this by implementing our proprietary SMM (Smart Maintenance Monitoring) system, allowing the operations team to monitor equipment performance in real time. The system also provides early-warning alarms, helping to prevent future failures and unplanned downtime.
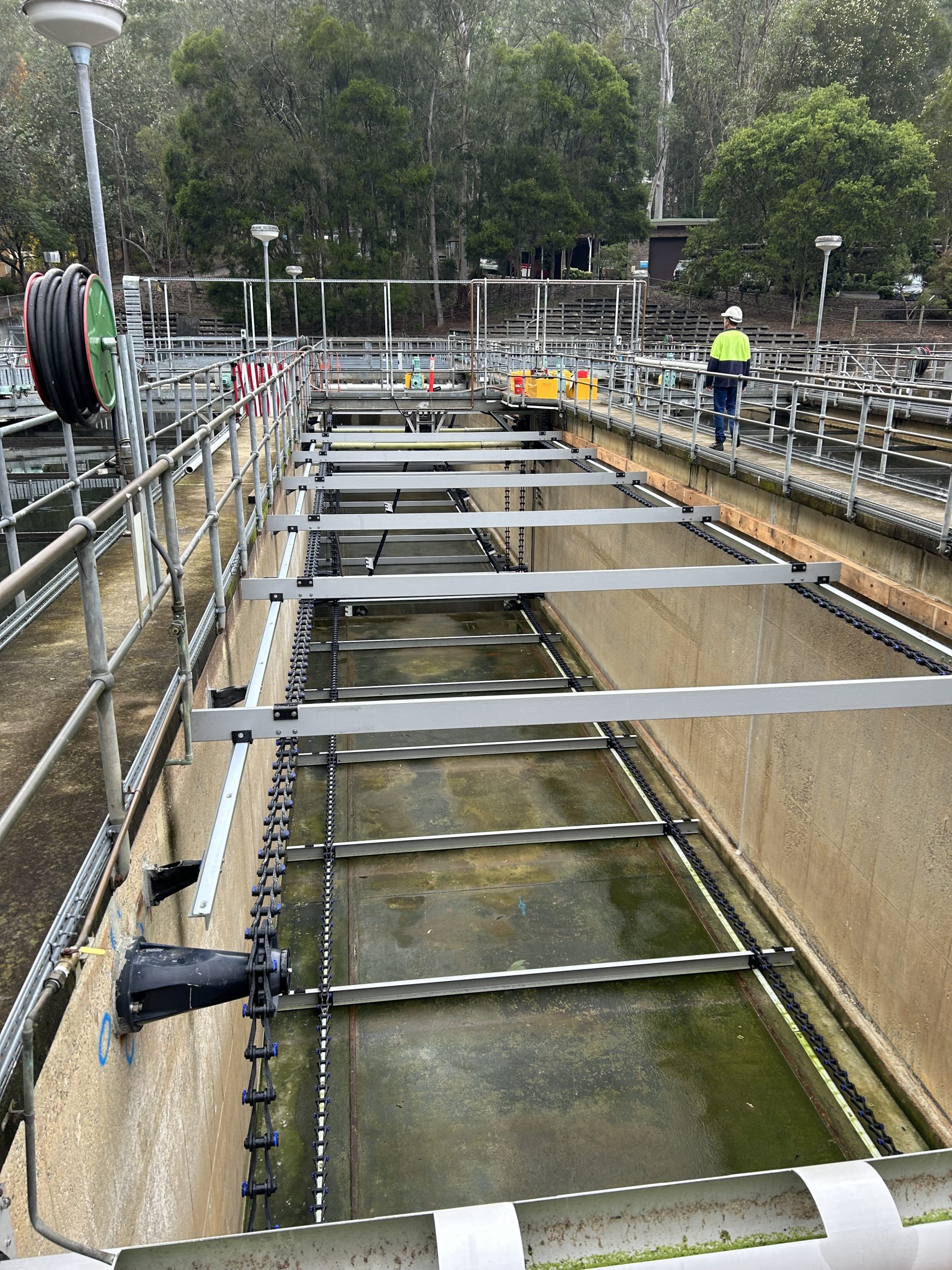
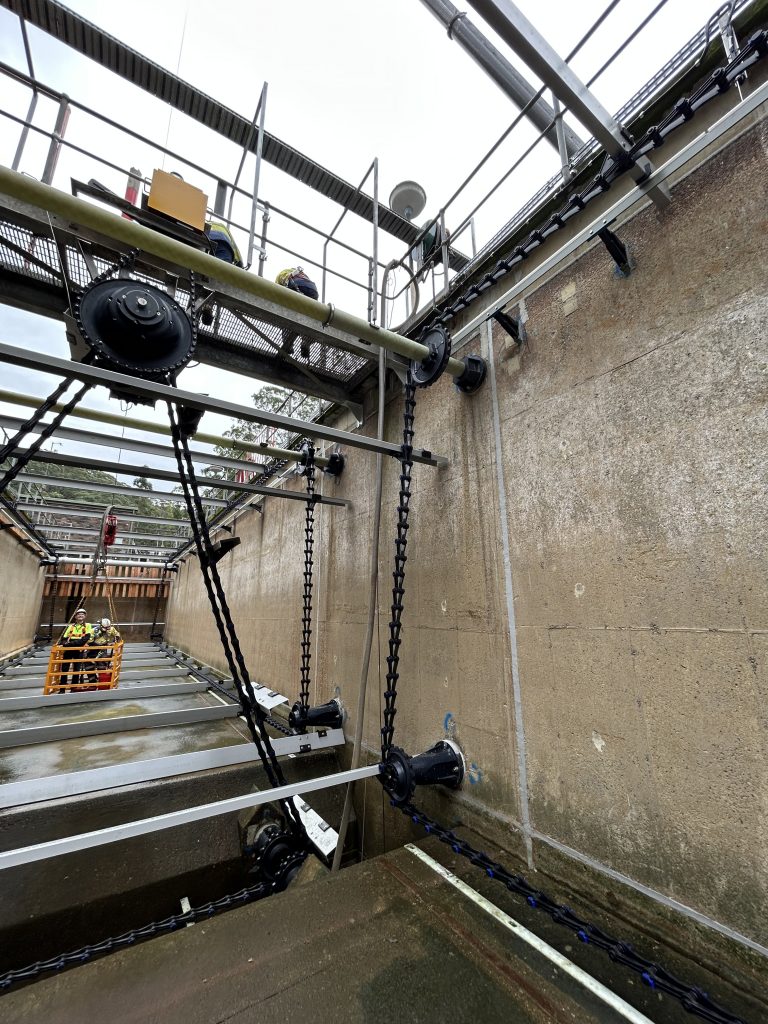
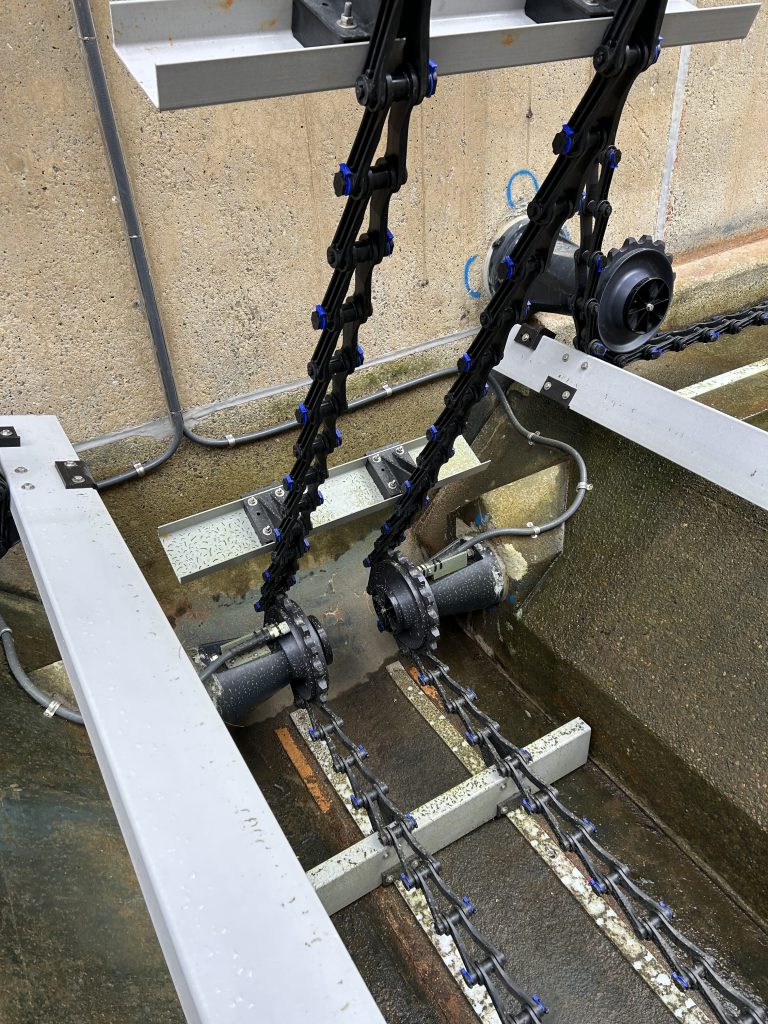
Outcome
The upgrade delivered a reliable, standardised solution that aligns with the client’s broader asset strategy. By using Polychem components already installed at other sites, inventory requirements were reduced, with ongoing support from TES and local stock held at our Lisarow, NSW warehouse. Full installation was backed by TES’s onsite service team, including all ITPs for quality assurance.
The removal of corroded steel shafts eliminated historical alignment issues, replaced with durable Polychem stub shafts and idler sprockets. Mechanical torque-limiters were added for overload protection, further improving system reliability.
The integration of the Polychem SMM (Sprocket Motion Monitoring) system into the client’s SCADA platform provided real-time visibility and fault alarms, helping to prevent equipment damage. Overall, the project has significantly improved operational uptime and reduced maintenance burdens associated with the aging system.